Drive types
The right drive for your project
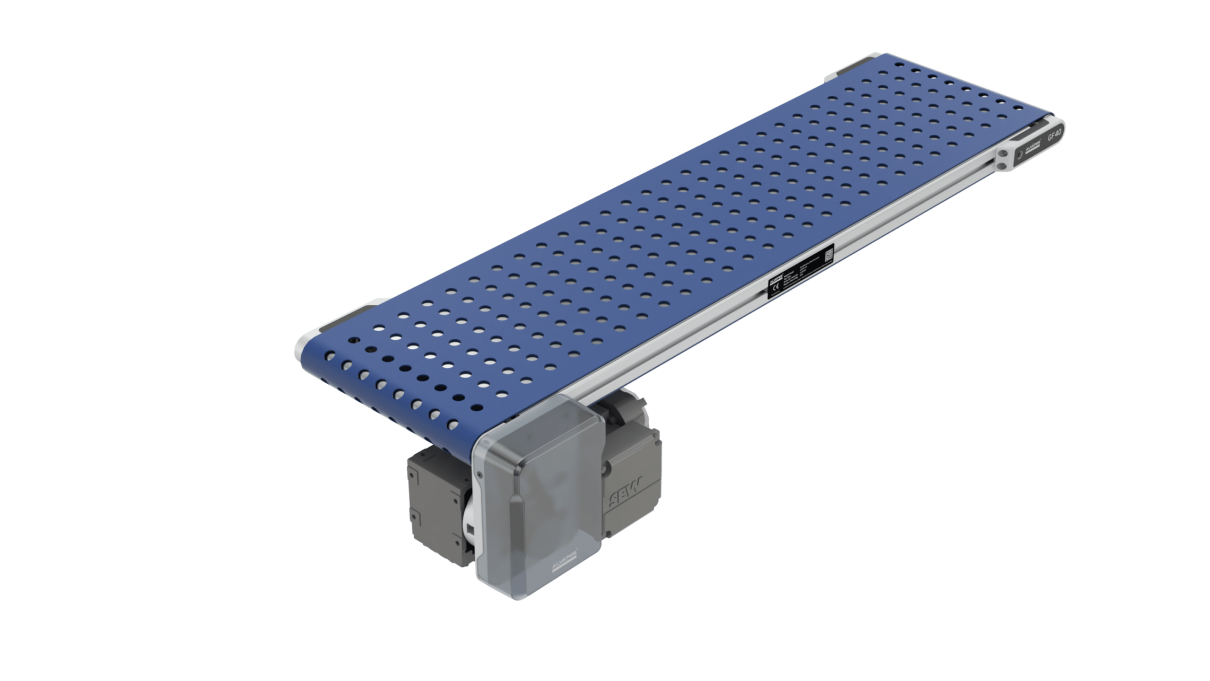
The ALVÁRIS belt conveyors are available with different drive types. Depending on the application, the following variants can be selected:
-
At Indirect drive the drive motor is positioned below the conveyor belt
-
At Direct drive the drive motor is positioned to the side of the conveyor belt
-
At Centre drive the drive motor is positioned centrally below the conveyor belt. The position along the length of the belt is variable.
-
At Drum drive the drive motor is located inside the drive roller
Indirect drive
With the indirect drive, the drive motor is positioned below the conveyor belt. It is connected to the drive roller by means of low-wear drive toothed belts. The indirect drive can be positioned on the left or right side of the belt.
The indirect drive is used when the drive unit should or must be located below the conveyor belt for space reasons.
Another advantage of this type of drive is that two pinion sizes are available. These allow the transmission ratio and thus the conveyor belt speed to be changed without changing the motor. The change can be made at any time.
In addition, the indirect drive allows the conveyed goods to protrude laterally over the belt, as all drive components are located below the belt edge. In the case of stable conveyed goods, this allows the belt conveyor to be narrower than the conveyed goods.
The disadvantages of the indirect drive compared to the direct drive are somewhat higher costs. In addition, transverse webs on the belt must not exceed a certain height, otherwise they would rub against the drive motor. The drive timing belt must also be visually inspected for damage or wear at specified maintenance intervals.
The indirect drive is used when the drive unit should or must be located below the conveyor belt for space reasons.
Another advantage of this type of drive is that two pinion sizes are available. These allow the transmission ratio and thus the conveyor belt speed to be changed without changing the motor. The change can be made at any time.
In addition, the indirect drive allows the conveyed goods to protrude laterally over the belt, as all drive components are located below the belt edge. In the case of stable conveyed goods, this allows the belt conveyor to be narrower than the conveyed goods.
The disadvantages of the indirect drive compared to the direct drive are somewhat higher costs. In addition, transverse webs on the belt must not exceed a certain height, otherwise they would rub against the drive motor. The drive timing belt must also be visually inspected for damage or wear at specified maintenance intervals.
Direct drive
With the direct drive, the drive motor is positioned to the side of the conveyor belt.
It is placed directly on the drive roller and fixed to it. Torque and backlash compensation are prevented by means of a torque support. The direct drive can be positioned on the left or right side of the belt.
The direct drive is used when the drive unit should or must be located next to the conveyor belt for space reasons.
Due to the smaller number of components, this form of drive is a cost-effective drive design. Furthermore, in comparison to the indirect drive, no visual inspection is required as there are no wearing parts. Furthermore, the direct drive has the advantage that transverse webs on the belt can be of any height - provided that the minimum deflection diameter is maintained.
Since only the speed provided by the gear motor is available, the variability of the speed is low. With very narrow conveyor belts, the laterally mounted motor can result in a tendency of the belt body to twist. This can be prevented with little additional effort by means of additional support.
In contrast to the indirect drive, it is also not possible for the conveyed material to protrude over the belt on both sides.
It is placed directly on the drive roller and fixed to it. Torque and backlash compensation are prevented by means of a torque support. The direct drive can be positioned on the left or right side of the belt.
The direct drive is used when the drive unit should or must be located next to the conveyor belt for space reasons.
Due to the smaller number of components, this form of drive is a cost-effective drive design. Furthermore, in comparison to the indirect drive, no visual inspection is required as there are no wearing parts. Furthermore, the direct drive has the advantage that transverse webs on the belt can be of any height - provided that the minimum deflection diameter is maintained.
Since only the speed provided by the gear motor is available, the variability of the speed is low. With very narrow conveyor belts, the laterally mounted motor can result in a tendency of the belt body to twist. This can be prevented with little additional effort by means of additional support.
In contrast to the indirect drive, it is also not possible for the conveyed material to protrude over the belt on both sides.
Centre drive
With the centre drive, the drive motor is positioned centrally underneath the conveyor belt. The position along the length of the belt is variable - if there is no specific requirement, positioning in the middle of the belt body is recommended. The motor can also be positioned on the left or right side of the belt.
The centre drive is used when
The centre drive is used when
-
the belt conveyor should have a fixed defined length,
-
a knife edge deflection is to take place on both sides,
-
there is no space for the drive unit at the side and below the belt at the infeed or outfeed.
As with the indirect drive, laterally protruding conveyed goods can be transported.
The disadvantages of the centre drive are
The disadvantages of the centre drive are
-
a higher and thus more cost-intensive effort, as more components are required compared to other drive variants,
-
extra effort in belt tracking adjustment, as more rollers are used in comparison
-
an increased space requirement underneath the belt
Drum drive
With the drum drive, the drive motor is located inside the drive roller
The space requirement on the side is limited to the cable outlet, which can be on the left or right side.
The drum drive is used when there is not enough space for the drive unit either at the infeed or outfeed or in the middle of the conveyor belt. The small space requirement is the most significant advantage of this drive.
The disadvantage of the drum drive is the limited service life due to the use of smaller components as well as the limitations in terms of speed and load possibilities.
The space requirement on the side is limited to the cable outlet, which can be on the left or right side.
The drum drive is used when there is not enough space for the drive unit either at the infeed or outfeed or in the middle of the conveyor belt. The small space requirement is the most significant advantage of this drive.
The disadvantage of the drum drive is the limited service life due to the use of smaller components as well as the limitations in terms of speed and load possibilities.
You have questions?
Please feel free to contact us with any questions you may have about our service portfolio or your orders.
+43 (0)5522 73011
info@alvaris.eu
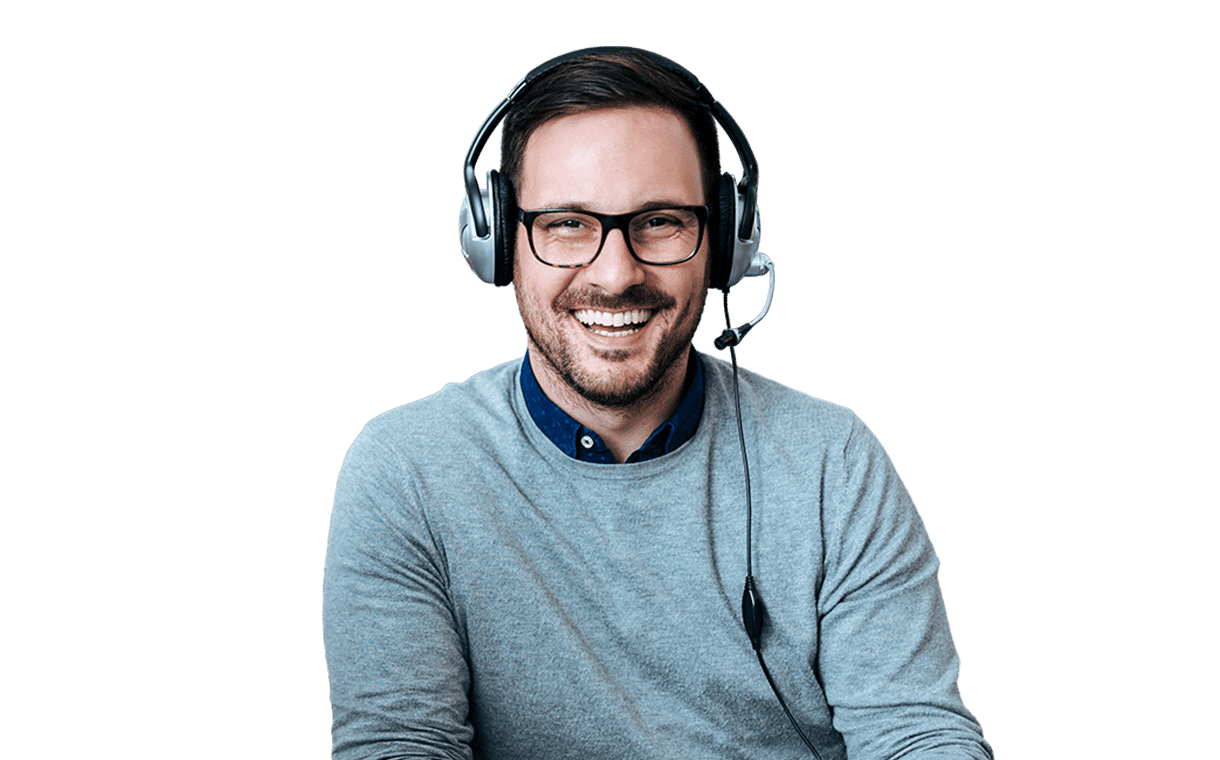